Open Gearing
Harness The Advantages of Open Worm Gearing
The many advantages of open worm gearing – such as its proven reliability, compactness for higher single reduction ratios, and the ability to withstand high momentary overloads – continue to make it attractive to machine designers as a means for power transmission. Worm gears provide large reduction ratios, low noise and vibration levels, and uniform angular velocity. The many advantages of open worm gearing – such as its proven reliability, compactness for higher single reduction ratios, and the ability to withstand high momentary overloads – continue to make it attractive to machine designers as a means for power transmission. Worm gears provide large reduction ratios, low noise and vibration levels, and uniform angular velocity.
Because worm gearing is so reliable and able to withstand repeated dynamic shock loading, it is ideal for applications in multiple industries. From steel and aluminum mills to paper mills, oil, lumber, and material handling, you’ll find Cleveland Gear open gearing on mixers, fans, conveyors, cranes, pulverizes, industrial truck axels, and pumps…the list goes on. Click here to go to our Standard Worm Gear Sets catalog for more information and specifications for well over 1,500 stock gear hobs. We offer the broadest range of worm gearing (3” to 54” CD) in the industry. If we don’t have the hob you need in stock, we’ll design and produce a custom hob in our facility. Our recess action hob designs and tangentially fed hobbing processes optimize the efficiency and power transmission of the gearset.
Designed for Quality
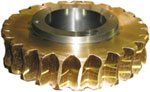
Worm Gear
Master Worm System – When a new gearset is introduced, Cleveland Gear designs and produces a master worm to match the hob form as well as worm thread plug gauge. This allows for future repeatability of the gear tooth geometry and worm thread form. Thus customers can replace a worm or worm gear individually, with high confidence that the “as initially produced” gear tooth form and contact is repeated for the replacement worm or gear.
Standardized Centrifugally Cast Bronze – Our engineers select the exact bronze alloy for our worm gears based on the application’s operational requirements. This ensures the most reliable gearset for the application is produced. Cleveland Gear also produces gears from customer specified materials, such as ductile iron, to meet the precise needs of their applications
Case Hardening – We select the proper steel alloy and heat treatment when the worms are to be case hardened. Cleveland Gear’s standard case hardening process is flame hardening. Other thru hardening or case hardening processes are available upon request. All of our worm threads are precision ground and subjected to non-destructive testing prior to shipment.
Click here to add your own text
Expanded Gear Production Capabilities – Cleveland Gear recently expanded its hobbing capabilities with the addition of three CNC gear hobbers. This expansion Increases our production capability of spur and helical gearing. Our most recent addition a 2.4 meter CNC gear hobber can produce high quality thru hardened and hobbed spur or helical gearing along with our largest worm gearing